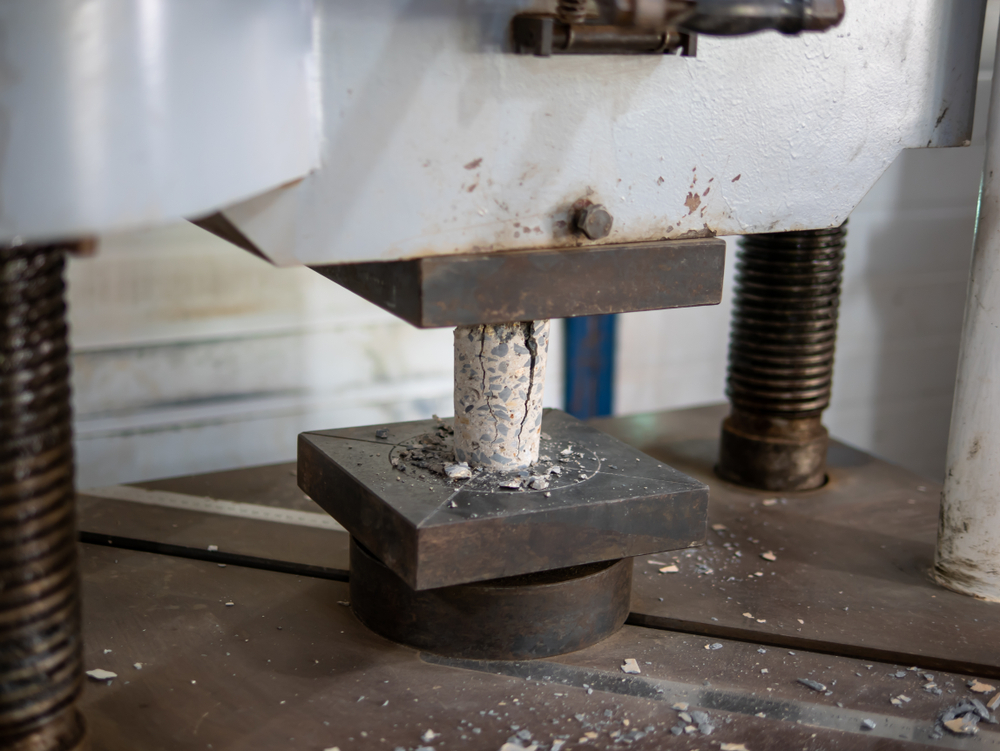
Testing Concrete Strength: A Guide to Cylinder Break Tests
Concrete is a foundational material used in construction due to its strength, durability, and versatility. However, ensuring that the concrete used in any structure meets the necessary strength requirements is crucial for safety and performance. One of the most common methods for determining the compressive strength of concrete is the concrete cylinder test. This guide provides an in-depth look at how to perform a concrete cylinder test, including the necessary procedure, equipment, and the importance of the results.
What is a Concrete Cylinder Test?
A concrete cylinder test is a standard procedure used to assess the compressive strength of concrete by testing molded concrete samples. These cylindrical samples are prepared and cured under controlled conditions, then tested using a specialized machine to measure the amount of force required to break them.
This test is widely used in the construction industry to verify that the concrete used in a project will be able to withstand the required loads and stresses. In most cases, the test results are used to ensure that the concrete meets the specified strength after 28 days of curing.
Why Testing Concrete Strength is Essential
Concrete is often subjected to a variety of forces, including compression, tension, and shear. Among these, compressive strength is the most critical factor in ensuring the durability and stability of structures. If concrete does not meet its required strength, it could lead to structural failure, putting both people and property at risk.
Performing a concrete cylinder test is vital for verifying the quality and strength of the concrete mix before it is used in construction. Additionally, the results of these tests can influence decisions regarding the acceptance or rejection of a batch of concrete, adjustments in the concrete mix, and compliance with design specifications.
How to Perform a Concrete Cylinder Test
Performing a concrete cylinder test requires several key steps to ensure accurate and reliable results. Below is a detailed concrete cylinder testing procedure that outlines the preparation, curing, and testing process.
Step 1: Sample Preparation
The first step in the concrete cylinder testing procedure is preparing the concrete samples. These are typically cylindrical molds with a standard size of 6 inches in diameter and 12 inches in height. The concrete mix used for the project is poured into these molds in layers, with each layer compacted to remove air pockets and ensure even distribution.
It’s essential to use proper techniques when filling the molds. The layers should be evenly compacted using a tamping rod or vibrating table to prevent voids and ensure uniformity. Once the molds are filled, they are smoothed at the top and left to cure.
Step 2: Curing the Cylinders
Curing is a critical part of the concrete strength test as it allows the concrete to gain its strength over time. Typically, the samples are cured in a controlled environment for 24 hours, after which they are removed from the molds. After demolding, the cylinders are stored in a curing tank or moist room at a constant temperature, usually around 73°F (23°C), and at a humidity of 95% or more.
The most common testing periods are after 7 days and 28 days of curing. The 7-day test provides an indication of early strength development, while the 28-day test gives a more accurate measure of the concrete’s final compressive strength.
Step 3: Testing the Cylinders
Once the concrete cylinders have cured for the designated period, they are ready for testing. The cylinders are tested using a concrete cylinder testing machine designed to apply a compressive load until the cylinder fails (i.e., breaks). This machine must be calibrated and in good working condition to ensure accurate test results.
Before the test begins, the technician centers the cylinder on the testing machine’s lower platen. A steel cap, sometimes with a neoprene pad, is placed on top of the cylinder to distribute the load evenly. The machine then applies a constant load to the cylinder at a specified rate until the concrete breaks. The concrete cylinder testing machine records the maximum force exerted on the cylinder before failure, which is used to calculate the compressive strength.
Concrete Cylinder Test Results
The results of a concrete cylinder test are typically reported as the compressive strength of the concrete, measured in pounds per square inch (psi) or megapascals (MPa). The strength is calculated by dividing the maximum load (force) applied by the cross-sectional area of the cylinder.
Interpreting Test Results
For most construction projects, the target compressive strength is specified in the design documents, usually after 28 days of curing. If the test results meet or exceed the specified strength, the concrete batch is considered acceptable. However, if the results fall short, the engineer may require additional testing, adjustments to the mix design, or, in some cases, rejection of the batch.
The typical range for standard concrete compressive strength is between 3,000 psi and 6,000 psi, though high-strength concrete can exceed 10,000 psi.
Common Factors Affecting Results
Several factors can influence the outcome of a concrete cylinder test:
- Curing Conditions: If the cylinders are not cured in the correct conditions (temperature and humidity), the concrete may not develop its full strength.
- Testing Machine Calibration: A miscalibrated machine can lead to inaccurate strength measurements. It’s essential to ensure the machine is regularly checked and calibrated.
- Concrete Mix: Variations in the mix proportions, such as the water-cement ratio or aggregate type, can affect the concrete’s compressive strength.
- Sample Preparation: Improper compaction or handling of the cylinders during preparation can introduce flaws, leading to lower-than-expected strength results.
The Importance of Using the Right Equipment
To perform an accurate concrete strength test, the correct equipment must be used, with the concrete cylinder testing machine being the most critical. These machines come in various types, but they all share the same fundamental purpose: applying a compressive load to the concrete sample.
Choosing a Concrete Cylinder Testing Machine
When selecting a concrete cylinder testing machine, several factors should be considered:
- Load Capacity: The machine must have the capacity to handle the expected range of concrete strengths.
- Accuracy: The machine should be precise and reliable, with a high degree of accuracy in load application and measurement.
- Ease of Use: The machine should be user-friendly, with features that simplify the testing process and minimize the chance of error.
Benefits of Concrete Cylinder Testing
The concrete cylinder test is widely used in the construction industry for several reasons:
- Accurate Strength Assessment: The test provides a direct measurement of the compressive strength of the concrete, which is essential for determining whether the material meets design specifications.
- Quality Control: Regular testing of concrete cylinders helps ensure consistent quality throughout a project, preventing the use of substandard concrete.
- Early Warning of Problems: Testing at intervals, such as 7 and 28 days, can provide early indications of potential issues with the concrete mix or curing process.
- Compliance with Regulations: Many building codes and standards require compressive strength tests to ensure the safety and integrity of concrete structures.
Conclusion
The concrete cylinder test is a critical procedure for assessing the compressive strength of concrete. By following the proper concrete cylinder testing procedure and using a calibrated concrete cylinder testing machine, construction teams can ensure that the concrete used in their projects meets the necessary strength requirements. This test plays an essential role in quality control, helping to prevent structural failures and ensuring the longevity of the structure.
Performing regular concrete strength tests is not only good practice but is often required by building codes and industry standards. Whether you’re a contractor, engineer, or quality control manager, understanding how to properly perform a concrete cylinder test is key to ensuring the safety and success of your construction projects.
Need Engineers and Designers in Hudson, CO?
Since 2006, High Plains Engineering & Consulting, LLC has been a civil and structural engineering company in Fort Lupton and the surrounding areas. We provide sensible solutions to geotechnical, structural, environmental, and civil engineering challenges. Our office provides practical expertise backed by diverse design resources to get the job done cost-effectively and efficiently with sustainability in mind. We offer various services for commercial, residential, and agricultural properties like soil testing, percolation testing, and foundation and septic design for new construction. Once that is taken care of we also offer services for floor framing, garage plans, house plans, site plans, and inspection services. Call us today for an appointment!
Categorised in: Concrete