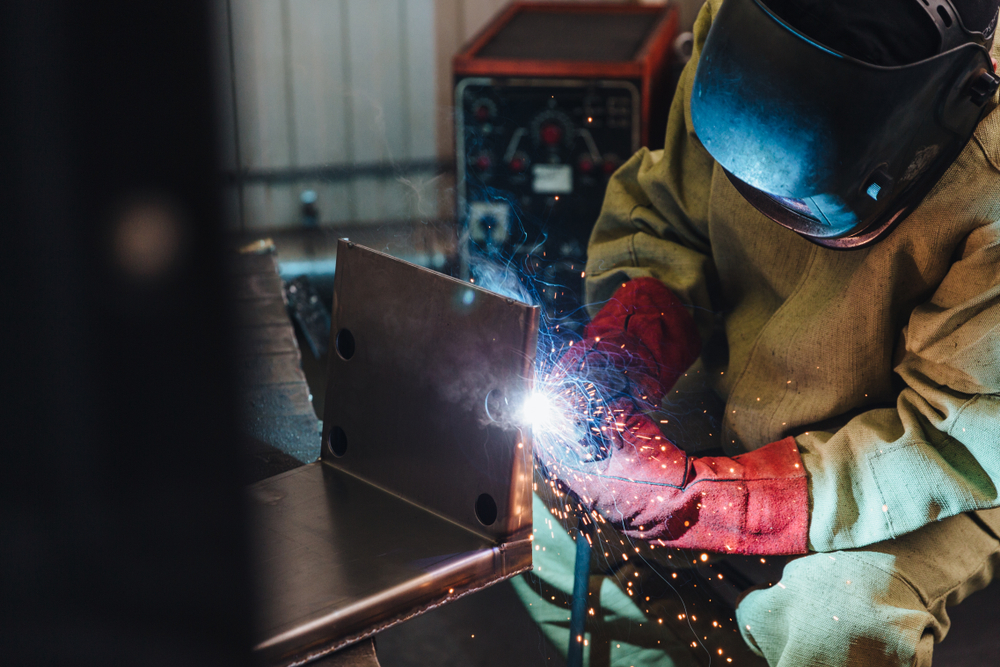
Fully Welding vs. Bolting Steel: Understanding the Key Differences
Steel is one of the most versatile and widely used materials in construction and manufacturing, thanks to its strength, durability, and flexibility. When it comes to joining steel components, two of the most common methods are welding and bolting. Each method has its unique advantages and disadvantages, which can significantly impact the performance and cost of a project. In this blog, we’ll explore the differences between welding and bolting steel, delve into the nuances of fully welding steel pieces, and provide insights into when one method might be preferable over the other.
Welding vs. Bolting Steel
What is Welding?
Welding is a process that involves the fusion of two or more pieces of metal by heating them to their melting points and allowing them to cool together. This creates a strong, permanent bond between the steel pieces. There are several types of welding techniques, including:
- MIG Welding (Metal Inert Gas): Uses a continuously fed wire and an inert gas shield to protect the weld area from contamination.
- TIG Welding (Tungsten Inert Gas): Employs a tungsten electrode and a filler material, with an inert gas shield to ensure a high-quality, clean weld.
- Stick Welding (Shielded Metal Arc Welding): Involves a consumable electrode coated in flux, which melts to form the weld.
What is Bolting?
Bolting is a mechanical fastening method that involves joining steel pieces using bolts and nuts. The process typically includes drilling holes in the steel components, inserting bolts through these holes, and securing them with nuts. This creates a detachable connection that can be easily assembled or disassembled.
Differences Between Welding and Bolting Steel
1. Strength and Durability
Fully Welding Steel Pieces: Welding generally provides a stronger and more durable bond compared to bolting. The fusion process creates a continuous joint with no gaps or weak points, resulting in a robust connection that can withstand significant stresses and loads.
Bolting Steel: While bolted joints can be strong, their strength depends on the quality of the bolts, nuts, and the precision of the hole alignment. Bolts can also loosen over time due to vibrations or thermal expansion, potentially compromising the integrity of the joint.
2. Cost and Time
Fully Welding Steel Pieces: Welding can be more expensive due to the cost of equipment, materials, and skilled labor. Additionally, welding processes can be time-consuming, particularly for complex or large-scale projects.
Bolting Steel: Bolting is often more cost-effective and quicker to execute. The process requires fewer specialized tools and less intensive training compared to welding. For projects where quick assembly and disassembly are essential, bolting can be a more practical choice.
3. Inspection and Maintenance
Fully Welding Steel Pieces: Welded joints often require rigorous inspection and testing, such as ultrasonic testing or X-ray inspection, to ensure there are no hidden defects. Maintenance of welded structures can be challenging if repairs are needed, as the weld might need to be cut out and re-welded.
Bolting Steel: Bolted joints are generally easier to inspect and maintain. Loose or damaged bolts can be replaced without affecting the surrounding structure. Regular inspection of bolts for signs of wear or loosening is essential to ensure the joint remains secure.
4. Flexibility and Design
Fully Welding Steel Pieces: Welding offers greater design flexibility, as it can be used to create complex shapes and configurations. It allows for seamless connections between components, which can be advantageous in applications requiring a smooth, uninterrupted surface.
Bolting Steel: Bolting is more suitable for modular or prefabricated designs where components need to be assembled or disassembled. It allows for easier modifications or adjustments to the structure, which can be beneficial in certain applications.
5. Aesthetics
Fully Welding Steel Pieces: Welded joints typically have a cleaner, more uniform appearance, especially when done with precision. The lack of external fasteners can result in a more aesthetically pleasing finish.
Bolting Steel: Bolted joints can be more conspicuous due to the presence of bolts and nuts, which may impact the overall appearance of the structure. However, in many industrial applications, the functional aspects of bolting outweigh aesthetic considerations.
Fully Welding Steel Pieces: Benefits and Considerations
Benefits
- Enhanced Strength: Fully welded joints provide a continuous connection with no interruptions, resulting in superior strength and load-bearing capacity.
- Seamless Integration: Welding allows for the creation of smooth, uninterrupted joints that can improve the structural integrity and appearance of the assembly.
- Reduced Maintenance: Properly executed welds can offer a lower maintenance profile compared to bolted joints, as there are no fasteners that can loosen or wear out.
Considerations
- Skill and Equipment: Welding requires skilled technicians and specialized equipment. The quality of the weld depends on the expertise of the welder and the condition of the equipment.
- Heat Affected Zone: The heat generated during welding can affect the properties of the steel around the weld area, potentially altering its strength or causing warping.
- Repair Challenges: Repairing a welded joint can be more complex than replacing a bolt, as it often involves cutting out the defective weld and re-welding the area.
When to Choose Welding Over Bolting
- High-Stress Applications: When the structure will be subjected to high stress or heavy loads, welding provides a stronger and more durable connection.
- Permanent Structures: For structures that are meant to be permanent and not subject to frequent disassembly, welding is often the preferred method.
- Aesthetic Considerations: If the appearance of the joints is important, welding can offer a cleaner and more seamless finish.
When to Choose Bolting Over Welding
- Modular Designs: For projects involving modular or prefabricated components that need to be assembled or disassembled frequently, bolting is more practical.
- Cost Constraints: When budget constraints are a significant factor, bolting can be more cost-effective than welding due to lower labor and material costs.
- Ease of Maintenance: If the structure requires frequent maintenance or adjustments, bolting allows for easier access and replacement of components.
Conclusion
Both welding and bolting are essential methods for joining steel, each with its own set of advantages and limitations. Understanding the differences between welding and bolting steel, and knowing when to use each method, is crucial for ensuring the success of a project. Fully welding steel pieces provides a strong, seamless connection ideal for permanent structures, while bolting offers flexibility, cost-effectiveness, and ease of maintenance for modular designs. By carefully considering the specific requirements of your project, you can make an informed decision and achieve the best results for your steel assembly needs.
Need Engineers and Designers in Hudson, CO?
Since 2006, High Plains Engineering & Consulting, LLC has been a civil and structural engineering company in Fort Lupton and the surrounding areas. We provide sensible solutions to geotechnical, structural, environmental, and civil engineering challenges. Our office provides practical expertise backed by diverse design resources to get the job done cost-effectively and efficiently with sustainability in mind. We offer various services for commercial, residential, and agricultural properties like soil testing, percolation testing, and foundation and septic design for new construction. Once that is taken care of we also offer services for floor framing, garage plans, house plans, site plans, and inspection services. Call us today for an appointment!
Categorised in: Steel