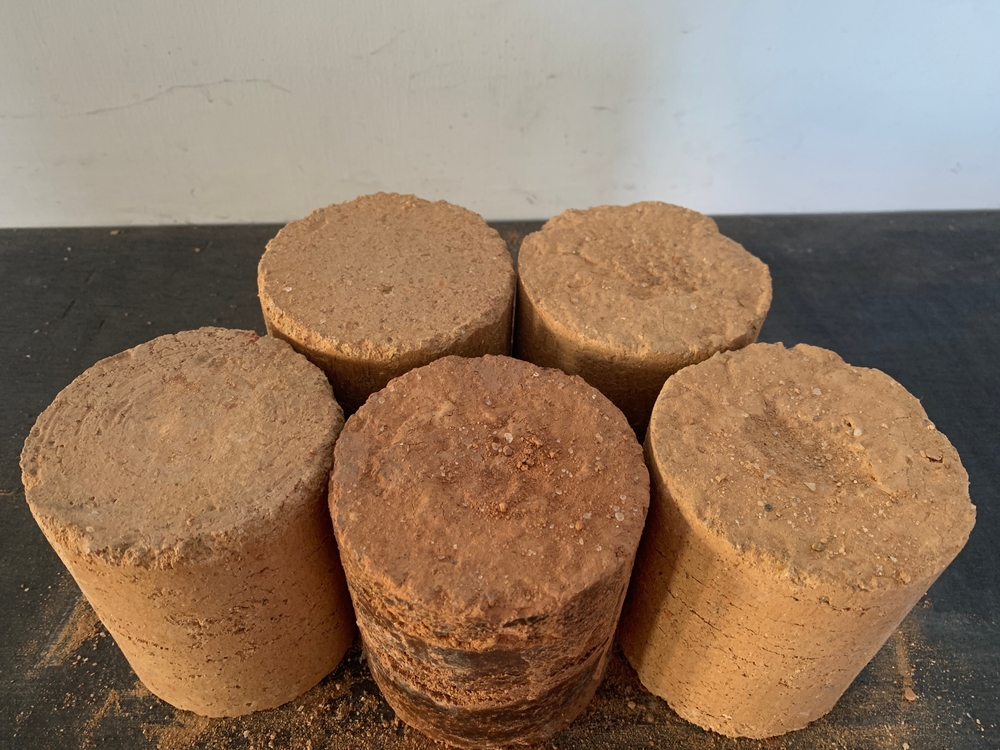
Why a Proctor Test is Crucial for Successful Construction Projects
In the realm of construction and geotechnical engineering, the significance of a Proctor test cannot be overstated. From preparing the foundation for towering skyscrapers to ensuring the durability of roadways, this essential soil compaction test lays the groundwork for structural stability. By examining the relationship between soil moisture and density, a Proctor test provides critical insights that contribute to the success and longevity of construction projects. This blog delves into the reasons why a Proctor test is important, its methodology, and its role in construction.
Understanding the Proctor Test
A Proctor test, named after engineer Ralph R. Proctor, is a laboratory method used to determine the optimal moisture content (OMC) at which a soil type achieves its maximum dry density (MDD). This is essential for ensuring that soil is compacted effectively before construction begins. The test involves compacting soil samples at varying moisture levels and measuring their densities, enabling engineers to identify the optimal conditions for compaction.
Types of Proctor Tests
There are two primary variations of the Proctor test:
- Standard Proctor Test: This method uses a lower compaction energy, suitable for projects with lighter load-bearing requirements.
- Modified Proctor Test: Employing a higher compaction energy, this method is ideal for projects requiring greater soil stability, such as highways and airport runways.
Each type caters to different construction needs, but the underlying principles remain the same.
Why Is the Proctor Test Important?
Soil compaction plays a pivotal role in the structural integrity of any construction project. Improperly compacted soil can lead to settling, cracking, and even structural failure. Here are the key reasons why the Proctor test is indispensable:
1. Ensuring Foundation Stability
One of the primary reasons for conducting a Proctor test before compaction is to ensure the stability of a structure’s foundation. By identifying the soil’s optimal moisture content and dry density, engineers can achieve a level of compaction that minimizes void spaces within the soil. This reduces the risk of uneven settling, which can compromise the structural integrity of buildings, bridges, and other infrastructures.
2. Preventing Soil Erosion and Settlement
Poorly compacted soil is highly susceptible to erosion and settlement over time. When soil erodes or settles unevenly, it can lead to costly repairs and project delays. The Proctor test provides a clear guideline for achieving compaction levels that resist these detrimental effects, ensuring the long-term durability of the construction site.
3. Optimizing Load-Bearing Capacity
Construction projects, particularly those involving heavy loads, require soil with a high load-bearing capacity. Conducting a Proctor test allows engineers to maximize the soil’s density, thereby enhancing its strength and ability to support substantial loads without deformation or failure.
4. Cost Efficiency
Without proper soil compaction, structures may require frequent maintenance or repairs, leading to increased costs over time. By conducting a Proctor test, engineers can prevent issues related to poor soil compaction, saving both time and money during and after construction.
5. Compliance with Geotechnical Standards
Many construction projects are subject to strict geotechnical engineering standards and regulations. The Proctor test ensures that soil compaction meets these standards, avoiding potential legal or safety issues that could arise from non-compliance.
How a Proctor Test Works
Understanding the procedure of a Proctor test can shed light on its importance and application. Here is a step-by-step overview of how this test is performed:
1. Soil Sample Collection
The process begins with collecting a representative soil sample from the construction site. The sample must be free of debris and organic matter to ensure accurate results.
2. Preparation of Soil Samples
The soil is dried and sieved to remove larger particles. This ensures uniformity in the sample, which is critical for accurate testing.
3. Addition of Water
Water is added to the soil incrementally, and the mixture is thoroughly blended. This step helps simulate various moisture conditions.
4. Compaction
The soil-water mixture is placed into a mold and compacted using a standard or modified energy level, depending on the type of Proctor test being conducted. The compaction is carried out in layers to replicate real-world conditions.
5. Measurement of Dry Density
The compacted soil is weighed, and its dry density is calculated. This process is repeated for different moisture levels to identify the moisture content at which the soil achieves its maximum dry density.
6. Analysis of Results
The data is plotted on a graph, with moisture content on the x-axis and dry density on the y-axis. The peak of the curve represents the optimal moisture content and maximum dry density.
Applications of the Proctor Test in Construction
The Proctor test is widely used across various types of construction projects. Its applications highlight why this test is a cornerstone of geotechnical engineering.
Road Construction
In road construction, ensuring proper compaction of the subgrade and base layers is critical for preventing issues like cracking and rutting. The Proctor test provides the necessary data to achieve the desired compaction levels, enhancing the longevity and performance of roads.
Foundation Design
Foundations for buildings and other structures rely heavily on well-compacted soil to bear loads effectively. The Proctor test ensures that the soil under a foundation can provide adequate support, reducing the likelihood of differential settling.
Earthworks and Embankments
Projects involving earthworks, such as embankments and levees, require carefully compacted soil to withstand environmental stresses. The Proctor test ensures that these structures are built on a stable and durable base.
Landfills
In landfill projects, proper soil compaction prevents the migration of contaminants and maintains structural stability. The Proctor test ensures that compaction meets environmental and geotechnical standards.
The Role of Geotechnical Engineering
Geotechnical engineering plays a vital role in modern construction by addressing soil and foundation-related challenges. The Proctor test is one of the many tools in a geotechnical engineer’s arsenal, but its significance is unparalleled. By providing precise data about soil properties, the test enables engineers to design and execute projects with a high degree of confidence in their structural integrity.
Challenges and Limitations
While the Proctor test is highly effective, it is not without its challenges and limitations:
- Soil Variability: Natural soil conditions can vary significantly across a construction site, making it challenging to obtain a truly representative sample.
- Time-Intensive: Conducting a Proctor test can be time-consuming, potentially delaying project timelines if not planned effectively.
- Field Implementation: Achieving laboratory-determined compaction levels in the field can be challenging due to equipment limitations and environmental factors.
Despite these challenges, the benefits of conducting a Proctor test far outweigh its drawbacks, making it an indispensable part of any successful construction project.
Conclusion
The Proctor test is a critical component of geotechnical engineering and construction planning. By identifying the optimal moisture content and dry density of soil, this test ensures proper compaction, which is essential for foundation stability, load-bearing capacity, and long-term structural integrity. Conducting a Proctor test before compaction not only enhances the durability of construction projects but also reduces costs and ensures compliance with regulatory standards.
Whether it’s a towering skyscraper, a robust highway, or a stable landfill, the importance of the Proctor test in construction cannot be overstated. As a cornerstone of geotechnical engineering, this test continues to pave the way for safer, more reliable infrastructure around the world.
Need Engineers and Designers in Hudson, CO?
Since 2006, High Plains Engineering & Consulting, LLC has been a civil and structural engineering company in Fort Lupton and the surrounding areas. We provide sensible solutions to geotechnical, structural, environmental, and civil engineering challenges. Our office provides practical expertise backed by diverse design resources to get the job done cost-effectively and efficiently with sustainability in mind. We offer various services for commercial, residential, and agricultural properties like soil testing, percolation testing, and foundation and septic design for new construction. Once that is taken care of we also offer services for floor framing, garage plans, house plans, site plans, and inspection services. Call us today for an appointment!
Categorised in: Proctor Tests