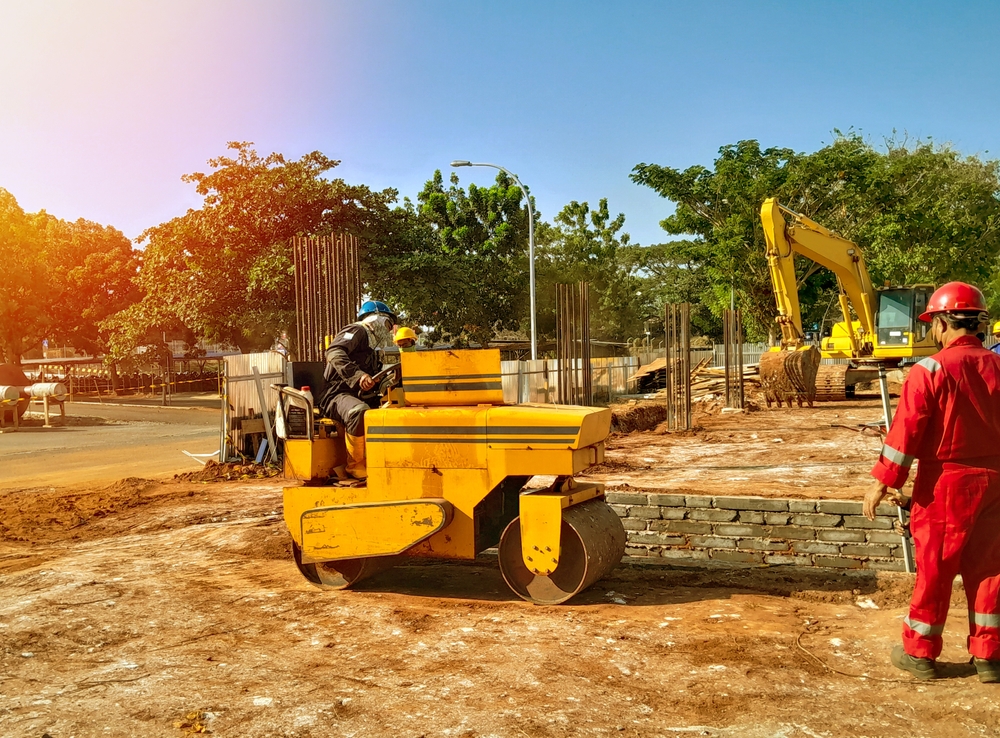
Ensuring Foundation Stability: Achieving the Right Compaction Percentage
When constructing a building, ensuring the stability and longevity of its foundation is paramount. A critical element in this process is achieving the correct compaction percentage for the soil beneath the foundation. Proper soil compaction not only strengthens the ground but also minimizes risks such as uneven settling and structural damage. This guide delves into the importance of soil compaction for foundations, foundation soil requirements, and soil compaction standards for foundations, helping builders and engineers establish a secure base.
Understanding Soil Compaction for Foundations
Soil compaction is the process of reducing the volume of air within the soil, making it denser and more stable. This is achieved through mechanical means, such as rollers, rammers, or vibratory plates. Proper compaction transforms loose soil into a firm foundation that can support the weight of structures, preventing problems like shifting or erosion.
Why Soil Compaction is Vital
- Load-Bearing Capacity: Compacted soil can better support the load of a structure, ensuring its stability.
- Minimizing Settling: Poorly compacted soil may settle unevenly over time, causing cracks and structural issues.
- Water Drainage: Proper compaction ensures better drainage, reducing water retention and minimizing risks of foundation damage due to swelling or shrinking soil.
Common Types of Soil for Foundations
Different soil types have varying behaviors and require unique approaches to compaction. Understanding foundation soil requirements is essential for determining the appropriate methods and standards:
- Sandy Soil: Highly drainable but may require careful compaction to avoid shifting.
- Clay Soil: Prone to retaining water, which can expand and contract; needs thorough compaction to ensure stability.
- Silt: Fine-grained and susceptible to water movement; compaction minimizes erosion.
- Gravel: Naturally stable and drains well but may require compaction to fill voids effectively.
Foundation Soil Requirements: Key Considerations
Choosing the right soil and ensuring its proper preparation are foundational steps in construction. Below are essential factors to consider:
Soil Testing
Before beginning construction, it’s crucial to assess the soil’s properties. Key tests include:
- Proctor Test: Determines the maximum dry density and optimal moisture content of the soil.
- California Bearing Ratio (CBR): Measures the soil’s strength.
- Atterberg Limits: Assesses the plasticity of soil, helping determine its usability for compaction.
Optimal Moisture Content
Achieving the right moisture level is critical for effective compaction. Too little moisture results in air voids, while excessive moisture leads to unstable soil. The ideal moisture content varies based on soil type but typically ranges between 8% and 20%.
Gradation and Compaction Layers
Soil should be graded and compacted in thin layers (usually 6-12 inches thick) to ensure uniform density. Each layer should be compacted before adding the next.
Soil Compaction Standards for Foundations
To ensure a durable foundation, adhering to soil compaction standards for foundations is essential. These standards dictate the degree of compaction and methods to achieve it.
Compaction Percentage
The correct compaction percentage for foundations typically ranges between 90% and 95% of the soil’s maximum dry density, as determined by the Proctor test. This percentage ensures the soil has enough strength to support the structure while maintaining stability over time.
Guidelines for Achieving the Correct Compaction Percentage
- Use the Right Equipment: Select compactors suitable for the soil type. For sandy soils, vibratory plates are effective, while cohesive soils like clay may require sheepsfoot rollers.
- Monitor Moisture Levels: Regularly test soil moisture and adjust as needed to achieve optimal compaction.
- Layered Compaction: Compact soil in thin, consistent layers, ensuring each layer reaches the required density.
- Field Testing: Conduct field density tests, such as the sand cone method or nuclear density gauge, to verify compaction levels.
Industry Standards
- ASTM Standards: The American Society for Testing and Materials (ASTM) provides detailed guidelines, such as ASTM D698 (Standard Proctor Test) and ASTM D1557 (Modified Proctor Test), for determining soil compaction levels.
- Local Building Codes: Always adhere to local regulations, which may have specific requirements based on soil conditions and structural needs.
What is the Correct Compaction Percentage for Foundations?
The correct compaction percentage for foundations is influenced by factors such as soil type, structure weight, and environmental conditions. While a general guideline of 90%-95% compaction is widely accepted, specific projects may require higher standards, especially for heavy structures or in areas prone to seismic activity.
Adjustments for Specific Conditions
- High-Rise Buildings: May require compaction levels closer to 98% to support greater loads.
- Seismic Zones: Soil may need to be compacted to higher densities to resist movement during earthquakes.
- Flood-Prone Areas: Ensuring proper drainage and stability necessitates meticulous compaction and moisture control.
Best Practices for Soil Compaction
Achieving the correct compaction percentage for foundations involves precision and adherence to best practices:
Conduct Pre-Construction Surveys
Evaluate the site’s natural soil conditions, identifying potential challenges such as high water tables, expansive soils, or contamination.
Choose the Appropriate Compaction Method
- Static Rollers: Suitable for granular soils.
- Vibratory Compactors: Effective for loose or sandy soils.
- Pneumatic Rollers: Useful for fine-grained soils like silt and clay.
Regular Testing and Quality Control
Ensure consistent testing throughout the compaction process. Use tools like:
- Penetrometers: To measure soil strength.
- Moisture Gauges: To monitor moisture levels.
- Nuclear Density Meters: For quick, on-site density measurements.
Troubleshooting Common Compaction Issues
Despite careful planning, challenges can arise during the compaction process. Here’s how to address them:
Over-Compaction
Excessive compaction can crush soil particles, reducing permeability and creating overly stiff soil that may crack under pressure. Adjust equipment settings or reduce compaction passes to mitigate this issue.
Insufficient Compaction
Failing to meet the required density can result in settling or instability. Reassess moisture content, compacting technique, and layer thickness to achieve better results.
Moisture Imbalance
If soil is too wet or dry, it can’t be compacted effectively. Use water sprays to add moisture or allow time for excess water to evaporate before continuing compaction.
Building a Strong Foundation
Ensuring the correct compaction percentage for foundations is a fundamental step in construction. Proper soil preparation enhances stability, minimizes risks, and extends the lifespan of a structure. By understanding soil compaction standards for foundations and adhering to foundation soil requirements, builders can create safe and resilient buildings. Regular testing, meticulous planning, and adherence to industry standards are key to achieving the best results.
Whether you’re constructing a home, commercial building, or infrastructure project, investing time and effort into proper soil compaction pays dividends in durability and safety. Remember, a strong foundation starts with the ground beneath it.
Need Engineers and Designers in Hudson, CO?
Since 2006, High Plains Engineering & Consulting, LLC has been a civil and structural engineering company in Fort Lupton and the surrounding areas. We provide sensible solutions to geotechnical, structural, environmental, and civil engineering challenges. Our office provides practical expertise backed by diverse design resources to get the job done cost-effectively and efficiently with sustainability in mind. We offer various services for commercial, residential, and agricultural properties like soil testing, percolation testing, and foundation and septic design for new construction. Once that is taken care of we also offer services for floor framing, garage plans, house plans, site plans, and inspection services. Call us today for an appointment!
Categorised in: Soil Compaction