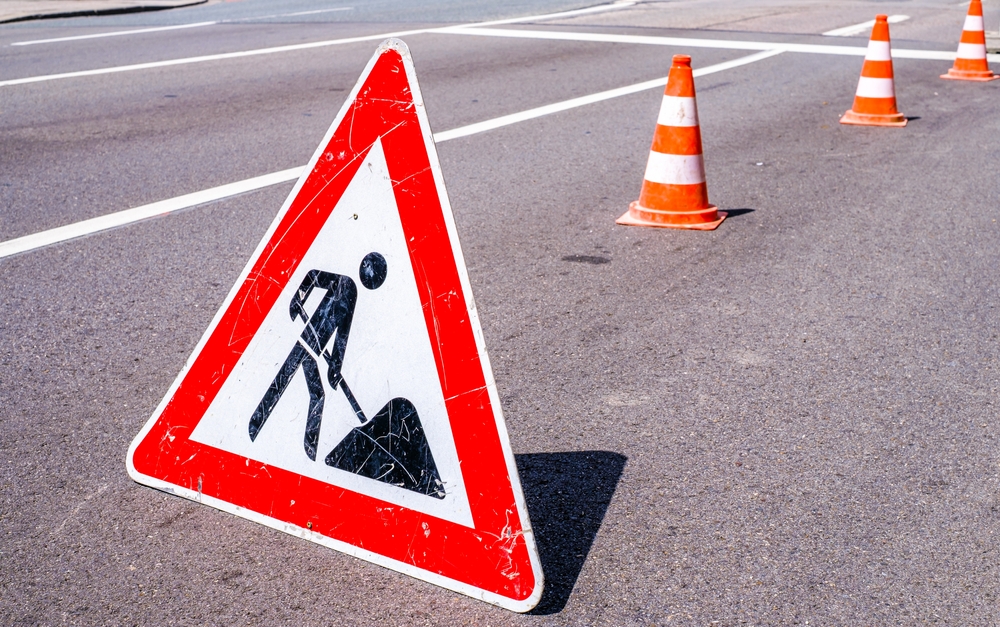
How to Use a Marshall Compactor Effectively
The Marshall compactor is an essential tool in the field of civil engineering and road construction, specifically designed for testing the properties of asphalt mixtures. Whether you’re a seasoned professional or a beginner in materials testing, understanding how to use a Marshall compactor effectively can save time, enhance precision, and ensure compliance with industry standards.
This blog provides a step-by-step guide on what is a Marshall compactor, its uses, and how to maximize its efficiency.
What is a Marshall Compactor?
A Marshall compactor is a laboratory device used to prepare compacted asphalt samples for stability and flow testing. This tool plays a critical role in determining the durability, strength, and suitability of asphalt mixes for road construction. Named after Bruce Marshall, the inventor of the Marshall mix design, the compactor is designed to mimic real-world conditions that asphalt experiences under traffic loads.
Components of a Marshall Compactor
- Compaction Hammer: A weighted hammer that delivers controlled blows to compact the asphalt mixture.
- Mold Assembly: A cylindrical mold where the asphalt mix is placed for compaction.
- Base Plate: Supports the mold during the compaction process.
- Automatic Controls (Optional): Some models feature automated systems to ensure uniform compaction.
Why is the Marshall Compactor Important?
The primary purpose of using a Marshall compactor is to prepare samples that simulate field conditions. These samples are then tested for stability (resistance to deformation) and flow (deformation under load). Without proper compaction, test results may not accurately represent the performance of the asphalt mix, leading to poor pavement quality.
By using a Marshall compactor effectively, you can:
- Ensure consistency in asphalt mix designs.
- Meet project specifications and standards.
- Enhance the quality and longevity of pavements.
Preparing to Use a Marshall Compactor
Before operating a Marshall compactor, it’s crucial to set up the equipment and materials correctly. Follow these preparatory steps to ensure smooth operation:
1. Familiarize Yourself with the Equipment
Read the manufacturer’s manual to understand the specific features of your Marshall compactor. This is especially important if you’re using a model with automated controls or unique components.
2. Gather Materials
You’ll need:
- Asphalt mixture
- Preheated mold and base plate
- Compaction hammer
- Release agents (e.g., talc or oil) to prevent the mixture from sticking to the mold or hammer.
3. Preheat the Mold
Preheating the mold to 93°C to 149°C (200°F to 300°F) ensures that the asphalt mix doesn’t lose heat during compaction. Proper temperature is critical for accurate compaction and testing.
4. Calibrate the Compactor
Check that the compactor delivers consistent blows with the correct energy. Calibration ensures repeatable results and compliance with standards like ASTM D6926 or AASHTO T245.
How to Use a Marshall Compactor: Step-by-Step Guide
Follow these steps for efficient and effective use of a Marshall compactor:
Step 1: Prepare the Asphalt Mix
Mix the asphalt binder and aggregates according to your project’s design specifications. The mixture should be homogenous and at the correct temperature, typically between 135°C and 165°C (275°F to 325°F).
Step 2: Assemble the Mold
Place the base plate on a stable surface and attach the cylindrical mold. Coat the interior of the mold and base plate with a release agent to prevent sticking.
Step 3: Fill the Mold
Pour the heated asphalt mixture into the mold in one or two layers, depending on the required specimen thickness. Level the top of the mixture with a spatula or trowel to ensure even compaction.
Step 4: Position the Mold in the Compactor
Place the filled mold onto the base of the Marshall compactor. Ensure it is aligned properly to avoid uneven compaction.
Step 5: Start the Compaction Process
Lower the compaction hammer into position. Depending on the standard being followed, apply a specific number of blows (e.g., 50 or 75) on each side of the sample. For automated models, simply set the number of blows and start the machine.
Step 6: Rotate the Mold and Repeat
Flip the mold to compact the opposite side of the sample. Apply the same number of blows to ensure uniform compaction.
Step 7: Remove the Specimen
Allow the compacted specimen to cool slightly before removing it from the mold. Use an extractor if necessary to avoid damaging the sample.
Tips for Effective Use of a Marshall Compactor
To get the best results, keep the following tips in mind:
Maintain Consistent Temperature
Temperature control is crucial for accurate results. Always preheat the mold and maintain the asphalt mixture within the recommended range.
Use Proper Safety Gear
The compaction process involves high temperatures and mechanical operations. Wear heat-resistant gloves, safety goggles, and other protective equipment.
Clean the Equipment Regularly
Residue from asphalt mixtures can accumulate on the mold and hammer, affecting performance. Clean the equipment after each use to prevent build-up and ensure accurate compaction.
Check for Wear and Tear
Inspect the compaction hammer and other components for wear. Replace any damaged parts promptly to maintain accuracy.
Common Challenges and How to Overcome Them
Inconsistent Specimen Thickness
- Cause: Uneven filling of the mold or improper alignment.
- Solution: Ensure the mold is filled evenly and aligned properly in the compactor.
Sticking Mixtures
- Cause: Lack of release agent.
- Solution: Apply a sufficient amount of release agent to the mold and hammer before use.
Overheating the Mixture
- Cause: Prolonged heating of the asphalt mix.
- Solution: Monitor the mixture’s temperature closely and avoid extended heating.
Applications of a Marshall Compactor
The Marshall compactor is widely used in:
- Quality Control: Ensuring asphalt mixtures meet project requirements.
- Research and Development: Testing new asphalt formulations.
- Pavement Design: Verifying the suitability of asphalt mixes for specific traffic and environmental conditions.
By preparing consistent samples, the compactor helps engineers evaluate the stability and performance of asphalt pavements under load.
Conclusion
Mastering how to use a Marshall compactor is essential for anyone involved in asphalt testing and pavement design. By understanding what is a Marshall compactor and following best practices for its operation, you can produce high-quality samples that yield reliable test results. Whether you’re testing for stability, flow, or other properties, effective use of this tool ensures the durability and safety of roadways.
By maintaining proper calibration, temperature control, and equipment cleanliness, you’ll not only enhance efficiency but also contribute to the overall success of your construction projects.
Need Engineers and Designers in Hudson, CO?
Since 2006, High Plains Engineering & Consulting, LLC has been a civil and structural engineering company in Fort Lupton and the surrounding areas. We provide sensible solutions to geotechnical, structural, environmental, and civil engineering challenges. Our office provides practical expertise backed by diverse design resources to get the job done cost-effectively and efficiently with sustainability in mind. We offer various services for commercial, residential, and agricultural properties like soil testing, percolation testing, and foundation and septic design for new construction. Once that is taken care of we also offer services for floor framing, garage plans, house plans, site plans, and inspection services. Call us today for an appointment!
Categorised in: Roadway Design